Sometimes size does matter
MFC-G Large Diameter GRE/GRP/FRP Firestop Collars massive size update!
Early this year, we were asked to find a solution for large ships such as Cruise ships, Ferries, Tankers and merchant ships that need to install EGCS (Exhaust Gas Cleaning System) using huge composite pipes to handle the treatment of sea water.
The size of the composite pipes, used on this project, is up to DN1000, meaning a impressive 1050 mm outer diameter and the Engineering team was wondering how they could find a new and innovative solution to achieve the fire stopping on fire divisions required by class where pipes are passing through fire rated divisions.
Our product, named MFC-G – Large Diameter FRP/GRE/GRP Firestop Collars, is the perfect solution for this, but, until recently, there was still a considerable limitation on the maximum approved size. The MFC-G Collars had already been tested and certified for steel deck and bulkhead installation, for pipes with an outer diameter up to 746mm, already the biggest collars in the market. We were approached by a major cruise line’s Engineering Team that required a much larger collar. We were asked to solve the size limitation and get the product tested and approved by an Agency within 3 months. This is very short amount of time as normally these Engineering projects take 6 to 10 months to complete. So now suddenly a larger size mattered.
Testing in a world that suddenly came to a halt:
As STI Marine Firestop’s core business is to find solutions to help our customers, we started to investigate the possibility to expand the range of our MFC-G Collars up to the DN1000 size. Our Engineering teams started to develop the technical drawings and bill of materials in order to organize the bulkhead and deck fire tests, as soon as possible.
As a leading company in the development of new fire stopping solutions, we are constantly conducting testing at our own fire testing facility and at fire labs all over the world. Because of this, we were able to work closely with one of the third-party fire labs and quickly arrange the construction of two specimens so that we could work within the time frame that we were given.
One of the most critical parts of the project was to produce the two massive collars, as our production was already filled up with ongoing orders. Our Production and Engineering teams were committed to make this critical project work, and they were able to have it manufactured in less than two weeks and ready to be shipped to the fire lab.
The very large DN1000 pipes, that would be fitted inside the collars, were supplied by our customer that is well immersed in the scrubber market as a composite pipe supplier. STI Marine Firestop selected to test at RINA’s Fire Testing Facility in Genoa, Italy, since their first available test dates would allow the tight schedule to be kept. The workshop at RINA moved quickly to construct the deck and bulkhead samples and provided assistance for the installation of the pipes and collars.
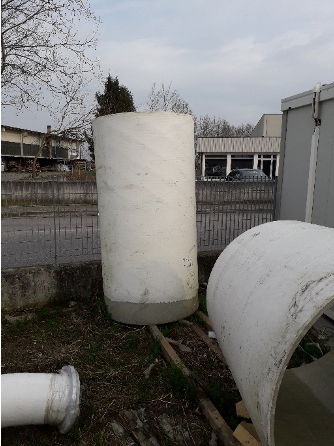
Composite pipe tested
We were on schedule throughout the project but, at the end of the week before the fire tests, the outbreak of COVID-19 became a reality in Italy and soon after in all the European countries, but despite this terrible event, we were able to manage the completion of the specimen’s construction and the two fire tests.
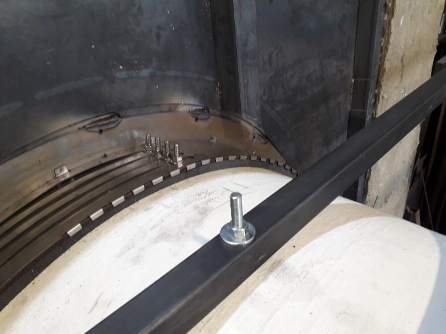
Bulkhead and deck installation
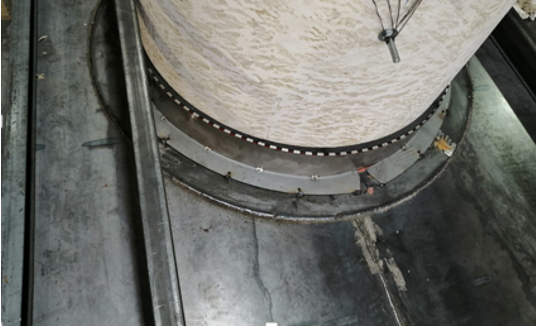
Bulkhead and deck installation
So, what do these ultra large MFC-G pipe collars replace?
The conventional method is to apply a very high-grade steel pipe section with flanges and often valves. This is typically in SMO steel, which is expensive, has long lead times and is fabricated specifically for these projects. The logistics can be a nightmare as these very heavy pipe sections need to be lowered into the ship using cranes.
By installing the MFC-G Collars, there are several advantages:
- Composite Pipes are run Continuously – Reduces the number of composite pipe sections and coupling flanges.
- Reduced Maintenance – Continuous composite pipes eliminates periodic maintenance of the steel pipe sections
- Simplified Logistics – Collar installations may be done independent of the pipe installation, eliminating staging conflicts.
- Reduced Weight – Our largest collar is only 14 kg, offering a lightweight alternative to sections of steel pipe weighing several hundred kilograms
- Easy to Install – Lightweight, split design allows for easy installation and adjustment
- Reduced Welding – Collars secured to division from one side via stitch welds or screws, as opposed to continuously welding steel pipe on both sides